解决氢氧化镁在电缆料中分散难题的五大方案
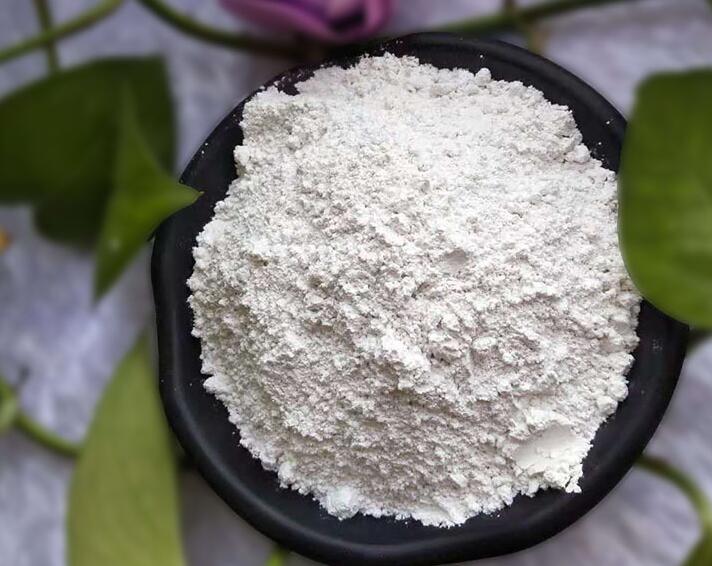
氢氧化镁(Mg(OH)₂)作为一种高效、环保的无机阻燃剂,在电缆料中的应用日益广泛。然而,其高表面能、强极性以及与聚合物基体的相容性差等问题,常导致其在加工过程中分散不均,进而影响电缆的阻燃性能、力学性能及表面光洁度。如何实现氢氧化镁在电缆料中的均匀分散,成为行业技术攻关的焦点。本文从材料改性、工艺优化、配方设计等维度,系统解析五大解决方案,为提升氢氧化镁分散性提供实践指导。
一、表面改性处理:提升相容性的核心手段
氢氧化镁的极性强、表面活性高,易在聚合物基体中团聚。通过表面改性可有效降低其表面能,增强与树脂的界面结合力。
1. 偶联剂改性技术
- 硅烷偶联剂(如KH - 550、KH - 570):水解后生成硅醇基,与氢氧化镁表面的羟基反应,形成化学键合。同时,另一端有机链段与聚合物缠绕,显著提升界面相容性。
- 钛酸酯偶联剂(如NDZ - 201):适用于高填充体系,通过单烷氧基与氢氧化镁结合,长链结构提供空间位阻,减少颗粒聚集。
- 应用要点:偶联剂添加量通常为氢氧化镁质量的1% - 3%,需通过高速混合设备实现均匀包覆,改性温度控制在80 - 120℃。
2. 表面活性剂处理
非离子型表面活性剂(如聚乙烯吡咯烷酮、硬脂酸盐)通过物理吸附降低颗粒间范德华力,改善流动性。适用于对成本敏感的中低端电缆料。
二、加工工艺优化:设备与参数的协同控制
分散效果与加工设备及工艺参数密切相关。通过工艺创新可突破传统混合的局限性。
1. 双螺杆挤出工艺升级
- 分段控温设计:进料段低温(150 - 160℃)防止预塑化,熔融段(170 - 190℃)强化剪切分散,均化段降温(160 - 170℃)减少热降解。
- 螺杆组合优化:采用“啮合块 + 反螺纹”组合,延长停留时间并增强分散剪切;填充率控制在70% - 80%以避免过度摩擦生热。
- 案例数据:某企业通过调整螺杆转速至300rpm、喂料速率匹配为60%,使氢氧化镁分散粒径从15μm降至5μm以下。
2. 预分散母粒技术
将氢氧化镁与载体树脂(如EVA、POE)预先制成高浓度母粒(60% - 70%含量),再与基料共混。此法可减少加工过程中的二次团聚,尤其适用于薄壁电缆生产。
三、分散助剂体系:协同增效的关键组分
通过添加功能性助剂,可构建“物理阻隔 + 化学键合”的多级分散网络。
1. 高分子分散剂
- 聚乙烯蜡(PE Wax):在熔融状态下包裹氢氧化镁颗粒,降低摩擦系数,促进流动分散。添加量0.5% - 1.5%。
- 超支化聚合物(HBP):三维立体结构提供空间位阻效应,抑制颗粒迁移团聚。
2. 纳米增强填料
纳米级二氧化硅、碳纳米管等可作为“隔离层”插入氢氧化镁团聚体,同时提升材料的抗冲击性能。
四、粒径与形貌调控:从原料源头优化分散性
氢氧化镁的初始粒径及形貌直接影响其分散行为。
1. 超细化与分级处理
- 采用气流粉碎或湿法研磨将D50控制在1 - 3μm,减少因粒径差异导致的沉降分层。
- 球形化处理(如熔融喷雾法)可降低比表面积,改善流动性。
2. 复合结构设计
通过水热法合成片状氢氧化镁/层状双金属氢氧化物(LDH)复合体,利用层间插层效应提升分散稳定性。
五、复配阻燃体系:降低填充量的新思路
通过复配协同阻燃剂减少氢氧化镁用量,间接改善分散性。
1. 磷 - 氮协效体系
次磷酸铝(AP)、三聚氰胺氰尿酸盐(MCA)等与氢氧化镁复配,形成致密炭层,实现阻燃增效(LOI可从28%提升至35%以上)。
2. 有机硅改性体系
苯基硅树脂与氢氧化镁复配,在燃烧时形成Si - O - Si网络结构,阻隔热量传递的同时提高分散均匀性。
结语:技术经济性的平衡选择
上述五大方案需根据电缆类型(如电力电缆、通信电缆)、阻燃等级(UL94 V - 0至V - 2)、成本预算等综合选择。例如:
- 高端特种电缆:推荐“表面改性 + 双螺杆工艺 + 纳米增强”组合方案,尽管成本增加8% - 10%,但可同步提升阻燃与抗拉强度(TS≥12MPa)。
- 普通建筑线缆:采用“预分散母粒 + 复配阻燃剂”方案,在保证UL94 V - 0级前提下,降低加工能耗15%以上。
随着纳米包覆技术、反应挤出工艺的进步,未来氢氧化镁