如何选择氢氧化镁提升电缆绝缘材料的耐火性
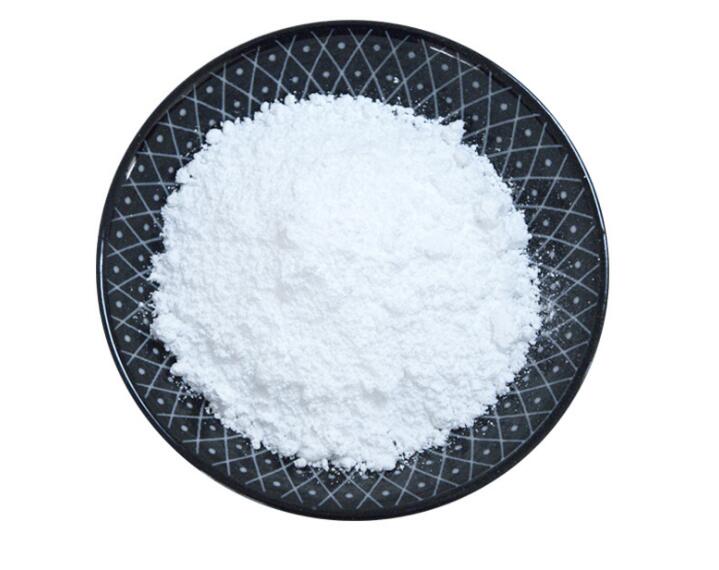
随着现代建筑、交通和能源行业对电缆安全性的要求日益严格,电缆绝缘材料的耐火性能已成为决定其市场竞争力与合规性的关键指标之一。在众多阻燃剂中,氢氧化镁(Magnesium Hydroxide, MH)因其环保、高效和成本可控的特性,被广泛用于提升电缆绝缘材料的阻燃性能。然而,如何科学选择氢氧化镁以满足不同场景下的耐火需求?本文将从材料特性、应用场景、工艺适配性及行业标准等维度,提供一套系统化的选择指南
一、氢氧化镁的阻燃机理与核心优势
氢氧化镁的阻燃作用主要通过以下机制实现
1. 吸热分解:在高温(约340℃)下分解为氧化镁和水蒸气,吸收大量热量,降低材料表面温度
2. 气相稀释:释放的水蒸气稀释可燃气体浓度,抑制火焰蔓延
3. 炭层保护:生成的氧化镁在材料表面形成致密炭层,隔绝氧气与热量传递
相较于传统阻燃剂(如氢氧化铝、卤系阻燃剂),氢氧化镁的优势包括
- 环保无毒:不含卤素,符合RoHS、REACH等国际环保法规
- 耐温性高:分解温度更高(340℃ vs. 氢氧化铝的220℃),更适合高温加工工艺
- 协同增效:可与氢氧化铝、纳米黏土等复配,提升阻燃效率
二、选择氢氧化镁的四大关键指标
1. 粒径与分散性
氢氧化镁的粒径直接影响其在聚合物基体中的分散性
- 纳米级(<1μm):分散性好,阻燃效率高,但成本较高,适用于高端电缆(如航空航天、核电领域)
- 微米级(1 - 10μm):性价比高,但需通过表面改性(如硅烷偶联剂处理)提升与聚合物的相容性
选择建议:普通电缆可选用改性微米级氢氧化镁;对机械性能要求高的场景优先选纳米级
2. 纯度与杂质控制
杂质(如CaO、Fe₂O₃)会降低阻燃效率并影响电缆绝缘性
- 工业级纯度(≥95%):适用于一般阻燃需求
- 高纯度(≥99%):用于高压电缆或高频通信电缆,避免杂质导致介电损耗
3. 表面改性工艺
未改性的氢氧化镁易团聚,导致加工困难。常用改性方法包括
- 硅烷偶联剂:提升与聚烯烃(如PE、PP)的界面结合力
- 硬脂酸处理:改善在PVC中的分散性,降低加工黏度
4. 添加比例与性能平衡
氢氧化镁的添加量通常需达到40%-60%才能实现UL 94 V - 0级阻燃,但过量添加会降低材料的机械强度和柔韧性。解决方案
- 复配技术:与氢氧化铝、膨胀石墨按5:3:2比例混合,可将总添加量降至30%-40%
- 纳米增强:添加2%-5%的碳纳米管或二氧化硅,补偿机械性能损失
三、工艺适配性:避免常见生产问题
1. 加工温度控制
氢氧化镁的分解温度(340℃)高于多数聚合物的加工温度(如PE的180 - 220℃),但仍需避免长时间高温剪切导致预分解
解决方案:采用双螺杆挤出机的低温混炼工艺,控制加工温度在200℃以下
2. 分散均匀性优化
团聚的氢氧化镁会形成“热点”,降低阻燃效果
检测方法:通过SEM(扫描电镜)观察分散状态;使用转矩流变仪监控加工稳定性
3. 吸湿性管理
氢氧化镁易吸湿,可能导致电缆绝缘电阻下降
对策:生产前对原料进行80℃×4h烘干处理;储存时使用防潮包装
四、测试验证与行业标准
1. 关键测试项目
- 阻燃性:UL 94垂直燃烧、极限氧指数(LOI)、锥形量热测试(热释放速率)
- 电气性能:体积电阻率、介电强度(需满足IEC 60502标准)
- 机械性能:拉伸强度、断裂伸长率(对比GB/T 2951.11)
2. 认证要求
- 建筑电缆:需通过BS 6387耐火等级(如CWZ级:950℃火焰+喷淋+震动)
- 轨道交通:EN 45545 - 2对烟密度和毒性有严格限制,需验证氢氧化镁配方是否符合R22/R23等级
五、应用案例与趋势展望
案例1:某高压电缆厂商采用硅烷改性的纳米氢氧化镁(添加量55%),使XLPE绝缘材料的LOI从19%提升至35%,并通过UL 94 V - 0认证,同时保持介电强度≥30kV/mm
未来趋势
- 超细化与功能化:开发粒径<100nm的氢氧化镁,减少对机械性能的影响
- 生物基改性:用腰果酚等天然物质替代传统偶联剂,提升可持续性
结语
选择氢氧化镁提升电缆耐火性时,需综合考量粒径、纯度、改性工艺及复配技术,并结合实际生产工艺进行适配性验证。随着环保法规趋严和高压/高频电缆