氢氧化镁填充量对电缆阻燃效率的影响规律——从机理到应用的全面解析
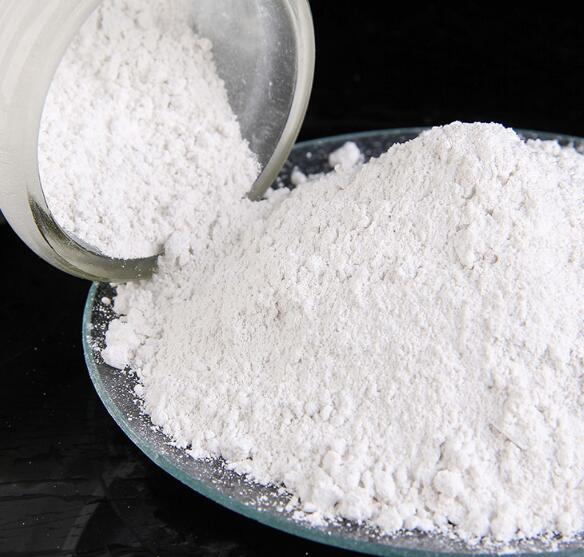
随着电力、通信和建筑行业的快速发展,阻燃电缆的需求日益增长。氢氧化镁(Mg(OH)₂)作为一种高效、环保的无机阻燃剂,被广泛用于提升电缆的阻燃性能。然而,其填充量的选择直接影响材料的阻燃效率、机械性能和加工成本。
一、氢氧化镁的阻燃机理与优势
氢氧化镁的阻燃作用主要通过以下机理实现:
1. 吸热分解:在高温(340℃以上)下,氢氧化镁分解为氧化镁和水蒸气,吸收大量热量,降低材料表面温度。
2. 稀释可燃气体:释放的水蒸气可稀释氧气和可燃气体浓度,抑制燃烧链式反应。
3. 形成保护层:分解后的氧化镁在材料表面形成致密屏障,隔绝氧气并阻止热量传递。
相较于传统卤系阻燃剂,氢氧化镁具有无卤、低烟、无毒的特点,符合欧盟RoHS、REACH等环保法规要求,是当前阻燃材料研发的热点方向。
二、填充量对阻燃效率的影响规律
研究表明,氢氧化镁的填充量与电缆阻燃效率呈非线性关系,需在阻燃性能、机械强度、加工性能之间找到平衡点。
1. 填充量过低(<30%)
- 阻燃效率不足:分解产生的吸热效应和气体稀释作用有限,难以达到UL94 V - 0或GB/T 18380.3标准。
- 案例数据:当填充量为20%时,氧指数(LOI)仅为24%,热释放速率(HRR)下降不足15%。
2. 填充量适中(40% - 60%)
- 最佳阻燃区间:此时氢氧化镁的吸热和屏障效应显著提升。例如,填充量50%时,LOI可提高至32%以上,HRR降低60% - 70%。
- 协同效应:与氢氧化铝(ATH)或纳米黏土复配,可减少填充量需求,同时改善材料韧性。
3. 填充量过高(>60%)
- 机械性能下降:过量填充会导致材料脆性增加,拉伸强度下降20% - 30%,影响电缆的弯曲寿命。
- 加工难度上升:高填充量使熔体流动性变差,挤出时易出现表面粗糙或气孔缺陷。
三、实验数据与行业标准验证
根据GB/T 2408 - 2021垂直燃烧测试和ASTM D2863氧指数标准,某型号无卤阻燃电缆的测试结果如下:
| 氢氧化镁填充量 | 氧指数(LOI) | 垂直燃烧等级(UL94) | 拉伸强度(MPa) |
|----------------|--------------|---------------------|----------------|
| 30% | 26% | V - 1 | 12.5 |
| 50% | 33% | V - 0 | 10.8 |
| 65% | 35% | V - 0 | 8.2 |
数据表明,填充量50% - 60%时可兼顾阻燃与机械性能。若需更高阻燃等级(如LOI>35%),建议采用表面改性氢氧化镁或与硅系阻燃剂复配,而非单纯提高填充量。
四、实际应用中的优化策略
1. 分阶段调整填充量
- 外层护套:填充量可提升至55% - 60%,优先满足阻燃要求。
- 内层绝缘层:填充量控制在40% - 45%,以保留柔韧性和电气性能。
2. 表面改性技术
- 通过硅烷偶联剂或硬脂酸对氢氧化镁进行包覆处理,可提高其与聚合物基体(如EVA、PE)的相容性,减少团聚现象,使填充量降低10% - 15%仍能达到同等阻燃效果。
3. 成本与性能平衡
- 氢氧化镁价格通常低于氢氧化铝,但密度较高。在满足阻燃标准的前提下,可计算单位体积成本,选择性价比最优方案。
五、未来研究方向
1. 纳米级氢氧化镁:粒径小于100nm的改性粉体可显著提升阻燃效率,减少填充量至35% - 40%。
2. 智能阻燃体系:开发与膨胀型阻燃剂(IFR)的协同配方,通过催化成炭反应增强屏障效应。
3. 生命周期评估(LCA):从原材料开采到废弃回收,量化氢氧化镁阻燃电缆的环境效益。
氢氧化镁填充量的选择是电缆阻燃设计中的关键参数,需综合考虑阻燃等级、机械性能、加工工艺及成本因素。通过实验验证与改性技术,行业可逐步实现“高效阻燃、轻量化、低成本”的平衡。未来,随着纳米技术与复配工艺的突破,氢氧化镁在阻燃电缆中的应用前景将更加广阔。
关键词:氢氧化镁填充量、电缆阻燃效率、氧指数、阻燃剂协同效应、表面改性技术